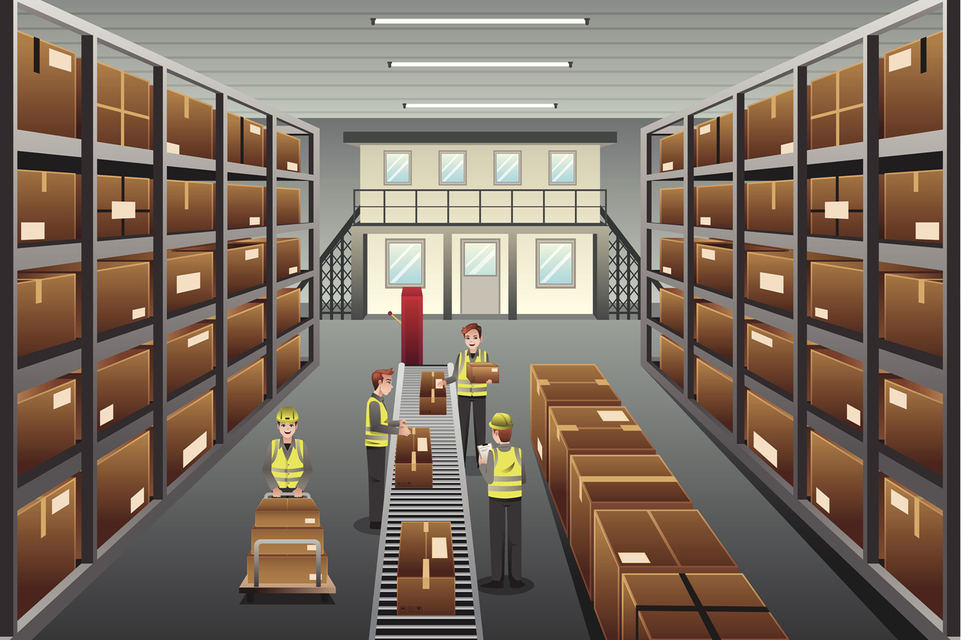
2 ambiti in cui è possibile incrementare la produttività nelle operazioni di magazzino
L'anno scorso abbiamo scritto un articolo con dei suggerimenti relativi al rinnovo estivo , con un'attenzione specifica ai problemi di sicurezza. Con la crisi sanitaria globale sostituita da nuove difficoltà, questa estate potrebbe essere il momento ideale per affrontare alcune sfide connesse alla produttività. Lo si potrebbe fare in risposta ai mercati in declino o a causa di crescenti opportunità di vendita, determinate, ad esempio, dal continuo aumento degli acquisti online.
Di seguito due aree in cui potreste migliorare la produttività del vostro magazzino:
1. Nuova valutazione della disposizione del vostro magazzino
I sei processi fondamentali del magazzino comprendono la ricezione, la disposizione, lo stoccaggio, il prelievo, l'imballaggio e la spedizione. Ognuna di queste aree offre opportunità di miglioramento dell'efficienza, ma il lay-out è influenzato da una miriade di fattori. In genere, si tratta dell'accumulo, delle dimensioni e dei volumi della gamma di prodotti, dei metodi di lavoro, dei tipi di attrezzature per la movimentazione dei materiali impiegati e delle dimensioni e degli spazi del magazzino stesso. Siate consapevoli, però, che le modifiche apportate in un'area potrebbero influire sulle operazioni previste più avanti nel flusso, quindi i cambiamenti devono essere effettuati con attenzione.
Per l'area di stoccaggio esistono diverse soluzioni di scaffalature. In un altro articolo abbiamo descritto i tipi di scaffalature, le loro funzioni e migliori applicazioni. Passando a scaffalature più alte e corridoi più stretti, in combinazione con i carrelli retrattili, è possibile ridurre l'ingombro dell'area, mantenendo la stessa capacità di stoccaggio. L'immagazzinamento a doppia profondità può permettere una densità ancora maggiore, ma richiede una gamma di prodotti più standardizzata, in quanto si perderà qualcosa sulla disponibilità immediata dei relativi pallet. Per ottenere il massimo dal vostro investimento, potreste valutare la possibilità di combinare lo stoccaggio ed il commissionamento degli ordini all'interno dello stesso sistema di scaffalature.
L'area di imballaggio dovrebbe essere vicina alla fine del processo di preparazione degli ordini e collegata all'area di spedizione. Si potrebbe anche decidere di riorganizzare e combinare entrambe le attività in un'unica sezione.
In conclusione, ogni processo può essere rivisto. Tuttavia, avrete la possibilità di iniziare a implementare i cambiamenti solo dopo aver mappato l'attuale flusso di merci e averle confrontate con quelle più vecchie. È una buona idea affrontare i sei processi una settimana alla volta, tenendo presente la loro interconnessione. Dopo aver completato questa fase di valutazione, è possibile sviluppare un piano d'azione.
2. Riesame delle strategie e delle risorse per il commissionamento degli ordini
Il cambiamento della tipologia degli ordini (un numero di ordini crescente e più piccoli) potrebbe costituire un buon motivo per esaminare attentamente le operazioni di commissionamento. In linea di massima, è possibile suddividere i relativi metodi di commissionamento in due tipologie: singolo e multiplo.
Quando il prelievo è per un singolo ordine, i dipendenti raccolgono le merci una ad una, in genere sui pallet di un transpallet. Con questa modalità è possibile prelevare e raccogliere in modo efficiente ordini di grandi dimensioni costituiti da molte linee d'ordine diverse. Chiedetevi: le merci provengono da aree diverse? In caso affermativo, invece di raccogliere l'intero ordine, il vostro addetto potrebbe adottare il metodo del picking a zone. Con questo sistema, ciascun operatore raccoglie una parte dell'ordine che poi scambia con gli altri.
Un'altra opzione è quella di raccogliere gli articoli degli ordini da aree diverse separatamente e combinarli nell'area di spedizione. Si tratta del cosiddetto consolidamento degli ordini. Risulta particolarmente utile se i prodotti di un ordine devono essere prelevati da una zona di magazzino refrigerata, fredda o "asciutta".
Con il prelievo multiplo, un unico dipendente raccoglie più ordini contemporaneamente per ridurre al minimo i percorsi a piedi. Il multi order picking può essere implementato in diversi modi. Con il sort-while-pick (scegli e preleva), i dipendenti raccolgono più ordini contemporaneamente e li smistano direttamente nei contenitori o nelle casse. In alternativa, direttamente all'interno dell'imballaggio della spedizione, quest’ultima modalità è nota come "pick-in-box".
Con il pick-then-sort (preleva e poi scegli), detto anche batch picking, più ordini vengono raccolti contemporaneamente e smistati successivamente in base agli ordini di vendita. Qual è la vostra attuale strategia? Il passaggio a uno dei metodi descritti potrebbe garantire una maggiore produttività?
Oltre a considerare le tecniche, potreste anche rivalutare le vostre attuali attrezzature per la movimentazione dei materiali. Invece dei transpallet o dei carrelli elevatori, l'uso di carrelli commissionatori dedicati potrebbe aumentare la produzione, offrendo anche vantaggi in termini di ergonomia. La riduzione della fatica e del disagio è un aspetto che i vostri dipendenti apprezzeranno molto!
- Punti di intervento
- Organizzate una riunione con i vostri fornitori di scaffalature e di movimentazione dei materiali per discutere il vostro nuovo progetto di flusso delle merci.
- Chiedete ai vostri dipendenti di contribuire al piano di cambiamento con i loro suggerimenti.
- Sviluppare un programma graduale per rendere il cambiamento pratico e realizzabile.